A Connected Environments MSc student does not need to look far to find an example of an Internet of Things (IoT) device which makes use of all of the technical skills we teach in the Connected Environments Master’s Programme.
We make use of the Prusa 3D Printers extensively to fabricate enclosures and supports for the devices we design and deploy in the wild. They are themselves a striking example of how each of the skills we teach come together in the creation of a full Internet-of-Things-connected machine, in this case a device that uses a plastic filament to print any 3D model you can imagine, layer-by-layer.
I will now discuss how all of the technical skills we teach come together in the 3D Printer: skills in electronics engineering, software engineering, and in digital fabrication.
Hardware
In the Connected Environments group, much of our work involves collecting highly localised data. This often requires designing bespoke sensor-based-systems to best collect data on the problem at hand. The problems are highly diverse due to the interdisciplinary nature of our group. Examples include the urban heat island effect in London (quantified using meteorological sensors), biodiversity in urban greenspaces (measured using sound sensors), and energy efficiency potential in buildings (as measured by human activity sensors).
Similarly, the 3D Printers from Prusa are embedded with sensors to quantify and prevent potential problems from occurring. One of these sensors monitors the internal temperatures of the components to minimise wear-and-tear and fire risk. Another is a proximity sensor to detect if a filament has been inserted, ultimately making the 3D Printers able to load the plastic filament automatically. All of these sensors are embedded in the printer using the same soldering techniques and PCB fabrication facilities that we have available and teach in our course.
Software
Software engineering plays a role in all the work that we do. This means that students who study with us will learn how to write embedded firmware to collect and send data from sensors, learn how to develop front-end interfaces using a mobile, web-based, or augmented reality (AR) application, and learn how to program the middle layers of the IoT stack. Our approach to 3D Printing at the Connected Environments Lab makes use of all these software layers.
The Prusa Firmware (the software embedded into the 3D Printers’ electronic circuitry), PrusaSlicer (the application to convert a 3D model into a printable set of layers), and OctoPrint (the web interface we have configured to operate the printers over the internet) are all open-source projects which are actively developed. We hope that our future students will look at these repositories. Even if large open-source projects are complex and take time to understand, there is much to be learned from reading through the documentation, even for those who are new to programming!
Digital Fabrication
We make heavy use of a variety of digital fabrication techniques (including 3D Printing, CNC milling, and Laser Cutting) to deliver high-fidelity prototypes and for our field-deployed devices. We pride ourselves in having the expertise to guide us towards the “best tool for the job” due to our placement in the world-leading UCL Bartlett faculty, which grants students and staff access to the fabrication resources present in the B-MADE Hub at Here East, in addition to new workshop facilities in UCL East.
Many of the components of the Prusa 3D Printers are printed using identical Prusa Printers. This means that should a part on our 3D Printers start to wear out, we can replace it simply by printing a new one! We have even conducted some of our own novel modifications on the printers to get them working reliably with multiple filaments at a time. More on that in a future blog post.
The future of 3D Printing in Connected Environments
These printers will remain upgradable by both students and staff in the Connected Environments group, whether by making the printing operations more reliable, by improving the user experience, or by streamlining their operation (for example, through predictive maintenance). A recent MSc student created a highly engaging, open-source Augmented Reality-based training for how to operate the 3D printers for their dissertation. Future 3D Printing projects are limitless, so if you’re interested, apply for the MSc here or contact us for information about other ways to collaborate.
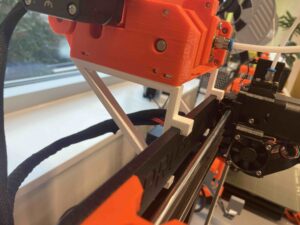
Recent modifications to the Prusa MMU, printed with white filament